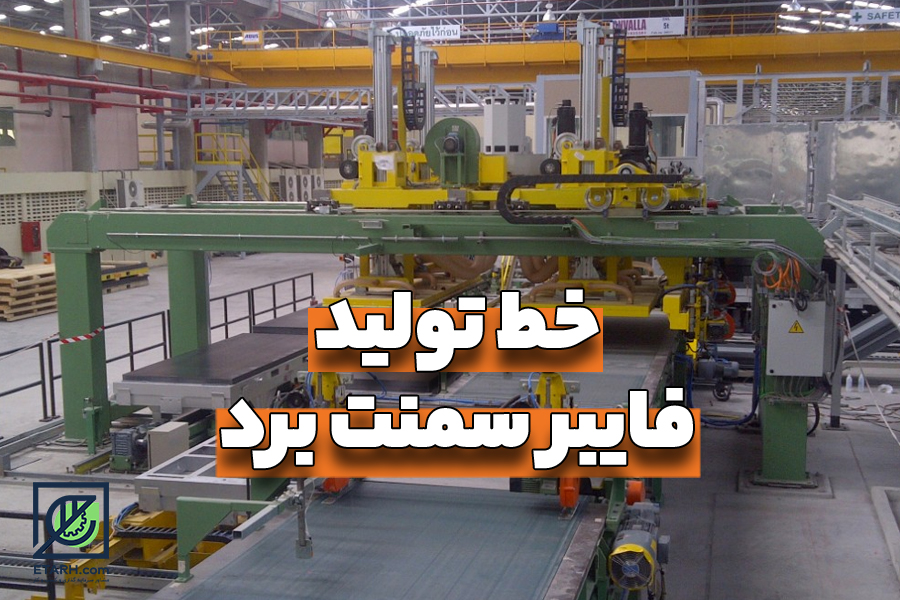
خط تولید فایبر سمنت برد
- 18 فروردین 1400
- ۰
- بازدیدها: 1,122
- دسته بندی:
خط تولید فایبر سمنت برد
بشر ، مسلح کردن با الیاف را از طبیعت آموخته است . یک نمونه خوب چوب است . در ساختمان چوب ، دو ماده لیگنین و هم سلولوز با مدول الاستیسیتۀ پایین و مقاومت کم وجود دارد که با الیاف سلولوز که مدول الاستیسیتۀ بالا و مقاومت زیادی دارند ، مسلح شده است . نتیجه این ترکیب چوب است که به عنوان مصالحی خوب , در ساختمان های چوبی و … مورد استفاده قرار می گیرد و دارای مقاومت کششی در حدود ۳۰ مگا پاسکال است .
مسلح کردن مصالح ساختمانی با الیاف گوناگون ، سابقه ایی بسیار کهن در تمدن های باستانی دارد . در گچ بری های دوران ساسانیان از موی اسب برای مسلح کردن استفاده شده است . همچنین از کاه برای مسلح کردن خشت استفاده شده است .در دوران جدید ، اولین سمنت بورد ها ، از سیمان آزبستی تهیه شدند که با ماشین Hatschek ایجاد شدند . ماشین هات چک در سال ۱۸۹۰ ساخته شد و توسط مخترع آن، لودویک هات چک به ثبت رسید که در ابتدا برای تولید صفحات سیمانی آزبستی استفاده گردید .این ماشین امروزه نیز به همان فرم اولیه مورد استفاده قرار می گیرد . هر چند که ماشین های هات چک امروزی از مدلهای قبلی بهره وری بیشتری دارند اما اگر مخترع آن امروز زنده بود این ماشین ها را می شناخت.امروزه انواع الیاف برای تقویت انواع مواد ( مثل پلیمر ها ، سرامیک ها و مواد سیمانی ) به کار می روند.
کامپوزیت های سیمانی ( از جمله فایبر سمنت برد ( ترکیبات سیمانی تقویت شده با الیاف هستند که حاوی سیمان و الیاف کوتاه یا بلند می باشند ( بدون سنگدانه ) . اما کامپوزیت های بتنی یا بتن تقویت شده با الیاف ، حاوی سیمان , سنگدانه و الیاف کوتاه هستند .بعد از کاربرد اولیه و بسیار زیاد آزبست ، محدوده وسیعی از الیاف دیگر نیز در سیمان به کار رفتند که شامل الیاف مدول بالا مثل فولاد , شیشه ، مثل کربن و کولار و الیاف مدول پایین مصنوعی ، مثل نایلون و پلی پرو پیلن و یا الیاف طبیعی مثل سلولز و کنف هندی می باشند .
از آنجا که کیفیت محصولات تولید شده آزبستی با فرآیند Hatschek با هیچ یک از محصولات مشابه قابل رقابت نبود ، علی رغم مشخص شدن سرطان زایی آزبست ، تا سال ها ی زیادی این محصول در کشور های پیشرفته نیز تولید می شد . در محدوده زمانی دهه ۱۹۷۰ تا اواخر دهه ۱۹۸۰ میلادی فناوری کاربرد الیاف غیر سمی و سازگار با فرایند Hatschek کشف شد . از آنجا که هیچ یک از الیاف طبیعی و مصنوعی به تنهایی تمامی خصوصیات آزبست را نداشتند ، بنابر این برای جایگزینی آزبست از هیبرید الیاف با مدول زیاد و کم به ترتیب , به عنوان تقویت کننده و کمک فرایند استفاده گردید.
مراحل تولید صفحات سیمانی الیاف دار در فرایند هات چک
فرایند تولید بر پایه تولید یک دوغاب سیمان، الیاف میباشد. پس از آن یک لایه نازک دوغاب روی صفحه نمدی نشسته و به کمک پمپها مکنده آبکشی میشوند. این لایهها به یک غلتک بزرگ (مندرل) انتقال یافته و پس از چند دور برداشت لایهها بر روی یکدیگر و رسیدن به ضخامت مورد نظراز غلظک جدا میشود. درصورتی که نیاز به تولید لوله باشد طول مندرل و قطر آن متفاوت بوده و تعداد برداشت دوغاب بسیار بیشتر خواهد بود. حال لایه جدا شده به هر شکل دلخواه (طرح دار، چین دار، مسطح و…) میتواند درآید. مرحله پایانی کار عمل آوری است که در دمای محیط و یا حرارت دهی(اتوکلاو) میتواند صورت گیرد. در ادامه به شرح کامل مراحل تولید خواهیم پرداخت .
مراحل تولید فایبرسمنت برد بشرح ذیل است:
۱-آماده سازی الیاف :الیاف سلولوز معمولا به شکل رول های کاغذ وارد خط تولید میشونداین مرحله الیاف وزن شده در حجم مشخصی از آب تر شده و به کمک پردههایی پخش میشوند و از طریق لوله هایی به میکسر اصلی منتقل میشوند.
۲- تهیه دوغاب سیمانی :دراین مرحله سیمان وزن شده به میکسر اصلی منتقل شد و با دوغاب الیاف وآب مخلوط میشود.این عمل تا زمانی که دوغابی یکنواخت شکل گیرد صورت میگیرد.
۳- شکل گیری لایه فیلم بر روی سیلندرهای مخصوص .این سیلندرها مشبک بوده و در حال چرخش در داخل دوغاب، یک لایه از دوغاب را برداشت کرده و در عین حال آب اضافی را از داخل خود به مجرایی برای بازیافت انتقال میدهند.
۴- انتقال لایه برداشت شده توسط غربال به نمد یکپارچه خشک . دراین حالت، نمد آغشته به دوغاب توسط غلتک هایی با کمک پمپهای مکنده، آبگیری نسبی شده و به مندرل منتقل میشوند.
۵- برداشت چند لایه فیلم از روی نمد تا رسیدن به ضخامت دلخواه وسپس جدا نمودن ورقه از روی مندرل.
۶ – پرس کردن ورقه ها برای افزایش مقاومت و رسیدن به ضخامت های مناسب . در این مرحله صفحات فلزی ما بین ورقه ها قرار داده شده و تعداد مشخصی از آنها با هم تحت فشار قرار گرفته و سپس از پرس خارج شده وصفحات فلزی از مابین ورقه ها بر داشته می شود .
۷- مرحله آخر تولید نیز عمل آوری است که در دمای محیط یا در تونلی که در آن رطوبت محیط حفظ میشود و یا دما بالاست , انجام میشود تا فرآیند عمل آوری سریعتر انجام گیرد. روش دیگر عمل آوری به کمک اتوکلاو است که دراین حالت، بخشی از سیمان با میکروسیلیس جایگزین میشود. البته برای کاهش هزینه سیستم،برخی اوقات بخشی از سیمان ممکن است با خاکستر بادی (Flyash ) نیز جایگزین شود.
مهمترین و بحرانی ترین مرحلهاین فرایند تشکیل فیلم است. خصوصیات لایهها به آهنگ فیلتر شدن لایه دوغاب از سیلندر مشبک به پشت نمد و همچنین آرایش یافتگی الیاف بستگی دارداین آرایش یافتگی به گونهای است که حتی استحکام ورقهها را در جهت طولی و عرضی متفاوت مینماید.
مشخصه های فیلتر نمودن نیز عاملی است که عملاً جایگزینی آزبست با الیاف دیگر را مشکل ساخته است. از آنجا که شبکهاین سیلندرها بسیار حساس بوده و در صورت هر گونه اشکال، مراحل برداشت لایه و انتقال آن به نمد با مشکل مواجه میشود، بنابراین باید از الیافی استفاده شود که با فرآیند موجود سازگارند و صدمهای به سیستم نزنند .
کنترل مشخصه های فیلتر نمودن در بخشهای آتی با توجه به ترکیب دوغاب و خصوصیات سطحی الیاف تشریح خواهد شد.
برایایجاد آرایش یافتگی الیاف در ورقه ها (که باعث بهبود خصوصیات مکانیکی میگردد) جریانی توسط همزنها در مخزن به وجود میآید که با توجه به جهت همزن، آرایش یافتگی خاصی را به وجود خواهد آورد. امااین عمل، اثر بدی در بهبود برداشت دوغاب توسط سیلندر مشبک خواهد اشت که در عملکرد ورقه سخت شده نیز اثر دارد.این اثر منفی، در اثر همزدن با سرعت بالا و استفاده از الیاف بلندتر، افزایش مییابد.
نکته دیگری که رعایت آن اهمیت زیادی دارد، درصد آب موجود در لایه برداشت شده از ظرف حاوی دوغاب(دیگ) بر روی نمد است. در صورتی کهاین مقدار بین ۲۲% تا ۲۸% تغییر نماید، استحکام بالا و پلاستیسیته لازم ( برای آنکه عملیات انتقال و شکل دهی بدون ترک خوردن یا تغییر شکل کنترل نشده انجام گیرد ) حاصل خواهد شد. بنابراین، محتوای آب لایهای که تازه شکل گرفته (که حدود ۵۵% است) باید به کمک پمپ خلا به حدود ۲۲-۲۸% کاهش یابد.
بدلیل اهمیت فرایند تشکیل لایه (فیلم) در دستگاه Hatschek به تشریح کامل این قسمت از فرایند می پردازیم.
فرایند تشکیل فیلم در ماشین Hatschek
موفقیت های بدست آمده در تولید فایبرسمنت بورد به وسیله ماشین هات چک به مقدار زیادی به تشکیل لایه های نازک کاغذ مانندی ( فیلم ) که بر روی هم قرار می گیرند تا ضخامت مورد نظر را بدست بدهند ، وابسته است .
این روش تولید باعث می شود تا الیاف در دو جهت پخش شوند تا مقاومت بهتری در صفحات بدست آید . مقاومت بدست آمده به وسیله این روش تولید تقریبا ۵۰ % بیشتر از صفحاتی است که تمام ضخامت صفحه در یک مرحله به روش ( Filter Press ) تولید می شوند .
تشکیل ورقه های در ماشین هات چک در ۴ مرحله انجام می شود .
۱-شکل گیری اولیه یک لایه فیلتر ( الیافی که در مرحله اول بر سطح غربال می نشینند و مانند فیلتر عمل می کنند ) در روی سطح غربال (Sieve)
۲-ساخته شدن یک لایه بسیار آب دار از سیمان الیاف دار بر روی لایه فیلتر که با چرخش غربال در تماس با دوغاب موجود در دیگ انجام می شود.
۳- آب گیری اولیه فیلم مرطوب با فشار کم ضمن انتقال بر روی تسمه نقاله (Flet )
۴- آب گیری شدید فیلم ضمن عبور از دهانه مندرل (Accumulation roller)
این مبحث مرحله دوم این فرایند را با جزئیات مورد بررسی قرار می دهد. با تعداد دیگهای ثابت( VAT) ، ضخامت لایه ای که هنگام عبور غربال ازدوغاب شکل می گیرد متناسب با جذر تراکم مواد جامد در دوغاب موجود در دیگ تقسیم بر سرعت ماشین می باشد. ارائه اطلاعات درباره نحوه کارکرد ماشین هات چک به خاطر اهمیت این رابطه است .این رابطه در خصوص کنترل صاف بودن صفحات و خصوصیات کلی ماشین در رابطه با ضخامت صفحات مورد بحث قرار می گیرد .
بخش اصلی ماشین هات چک از یک دیگ( Vat) پرشده با دوغابی از سیمان پرتلند و الیافی که قابلیت تشکیل لایه را دارند و یک غربال استوانه ای( Sieve )که در تماس با دوغاب درون آن می چرخد تشکیل شده است .
غربال استوانه ای روی محوری نصب شده و با یک نمد (Felt) که در بالای غربال پیچیده شده توسط یک غلطک جدا کننده (Couch roller) که روی آن قرار گرفته به حرکت در می آید.تسمه نقاله دور یک غلطک سندانی و یک غلطک انتهایی (مندرل ) پیچیده شده است.غلطک سندانی با فشار با مندرل در تماس است.
صفحات در ماشین هات چک بصورت زیر شکل می گیرند.
۱-هنگامی که غربال تمیز داخل دوغاب داخل دیگ فرو می رود ، آب دوغاب از غربال عبور کرده و یک فیلم نرم متخلخل از الیاف و سیمان روی سطح غربال بر جای می ماند.
۲-غربال حامل فیلم در هنگام خارج شدن از دیگ با تسمه نقاله نمدی که محکم دور غربال کشیده شده تماس پیدا می کند، بر اثر فشاراین تماس بیشتر آب فیلم گرفته می شود .
آب خارج شده به صورت یک جدا کننده عمل نموده فیلم جامد به تسمه نقاله نمدی انتقال پیدا می کند . این انتقال در واکنش به اثر گرفته شدن آب و همچنین به علت اینکه قدرت جذب فیلم توسط تسمه نمدی بیشتر از غربال است اتفاق می افتد .
۳-فیلم روی تسمه نقاله نمدی به سمت مندرل حمل می شود که درآنجا تحت فشار بیشترآبگیری نهایی انجام می شود .
۴-مقدار کافی از فیلم ها روی مندرل پیچیده می شوند تا یک ورقه ای با ضخامت مورد نظر را تشکیل دهند . سپس صفحات از مندرل جدا شده و به صورت تخت پهن می شوند .
فرایند آب زدایی لایه هایی که بر روی هم و تحت فشار قرار می گیرند باعث می شود که لایه ایی یک دست و ممتد ساخته شود که در مرحله بعد در اندازه های مشخص بریده می شوند.
همانطور که از ساختار ماشین هات چک انتظار می رود، امکان اندازه گیری ضخامت لایه ای که درون دیگ بر روی غربال رسوب می کند وجود ندارد . همچنین اندازه گیری ضخامت فیلم نرم قرار گرفته روی غربال در فاصله بین نقطه ای که تسمه نمدی با آن تماس پیدا می کندامکان پذیر نیست . علاوه بر آن اندازه گیری ضخامت فیلمی که بر روی تسمه نمدی بسوی مندرل حمل می شود ساده نیست . بنابراین می توان میانگین ضخامت فیلم را از ضخامت ورقه نهایی تقسیم بر تعداد فیلمهای تشکیل دهنده آن بدست آورد.
تجربه فشرده کردن ثانویه پس از شکل گیری ورقه به ما می گوید امکان مطالعه دقیق ساختار تشکیل صفحات ساخته شده وجود دارد. بنابراین می توان استنباط کرد که فشار شکل گیری در دهانه غلطک سندانی ومندرل بر ضخامت ورق نهایی و ضخامت ظاهری فیلم که در دیگ تشکیل می شود تاثیر می گذارد . امادر ادامه می توان دید که آب گیری فیلمها در درون ماشین هات چک موقعی که فیلم از غربال به تسمه نقاله نمدی انتقال می یابد تاثیر ناچیزی بر ضخامت فیلم خشک شده نهایی دارد. همچنین خواهیم دید که برغم اینکه ضخامت ورقه متاثر از فشار دهانه در مندرل می باشد اما این اثر ناچیز است.
وقتی که فقط اثرات اصلی بر نرخ شکل گیری فیلم را مورد توجه قرار می دهیم فشار دهانه را می توان نادیده گرفت که البته کمی از دقت عمل را می کاهد .
باید توجه نمود که ماشین های هات چک جدید ۴ یا تعداد بیشتری دیگ بصورت پشت سر هم دارند تا بهره وری افزایش یابد . نتایجی که در زیر ارائه می شود مربوط به ماشینی با ۴ دیگ می باشد که ۲ یا تعداد بیشتری از دیگهای آن بطور همزمان کار می کنند.
پس برای دست یافتن به نظریه رسوب فیلم لازم است فرض کنیم که شرایط در درون دیگ ها یکسان است . برغم این فرضیات ، نشان داده خواهد شد که پیش بینی دقیق ضخامت فیلم را می توان از ترکیب چیدمان و شرایط کارکرد درونی ماشین بدست آورد .
جزئیات مکانیزم شکل گیری فیلم
مکانیزم کلی شکل گیری فیلم از صافی گذراندن است. یک غربال استوانه ای در تماس با دوغاب از الیاف و سیمان می چرخد و فیلمی شکل می گیرد که بطور مدام از غربال که از دیگ بیرون می آید جدا می شود .
شکل گیری فیلم بصورت زیر انجام می شود
۱- لایه فیلترشده ایی از الیاف برسطح غربال در فاصله کوتاهی از غوطه ور شدن در آب شکل می گیرد. ( بلند بودن الیاف نسبت به دانه های سیمان باعث می شود که بر روی سطح غربال جمع شوند )
۲- فیلم در ادامه همچنان بر روی غربال جمع می شود اما به مرور که این حرکت ادامه پیدا می کند نسبت کمتری مواد الیافی و نسبت بیشتری مواد غیرالیافی بر روی سطح غربال جمع می شود . (بعد از این که یک لایه از الیاف بر روی سطح غربال جمع شد باعث چسبیدن مواد سیمانی بر روی لایه تشکیل شده از الیاف می شود )
۳- فیلم آبگیری شده از غربال جدا می شود و روی تسمه نقاله نمدی که غربال را حرکت می دهد قرار می گیرد . به این نکته باید توجه نمود که موقعیت شکل گیری لایه فیلتر(مرحله ۱) بستگی به طریقه عمل غلتک همزن الیاف در ماشین هات چک دارد که دو امکان می تواند در این رابطه وجود داشته باشد .
غلتک همزن الیاف درخلاف جهت غربال حرکت می کند و دوغاب را برروی غربال در بالای نقطه غوطه وری پرتاب می کند دراین حالت بیشترین مقدار شکل گیری لایه قبل از ورود غربال به مایع می باشد.
غلتک همزن الیاف درهمان جهت غربال حرکت می کند که ممکن است بایک زبانه حدود ۵۰ میلی متری لاستیک در زیر سطح مایع نصب شده باشددراین حالت لایه فیلتر درست زیر زبانه لاستیکی شکل می گیرد.
با توجه به نیاز معرفی مواد خام در این قسمت به صورت مختصر به معرفی مواد تشکیل دهنده می پر دازیم . در فصول آینده به تشریح کامل مواد خام می پر دازیم .
مواد
خوراک ماشین هات چک دوغابی است از الیاف ، سیمان پرتلند و مواد معدنی کاملا نرم شده مخلوط با آب .
الیاف
الیاف آزبست ( پنبه سوز) در فرمولاسیون اولیه بکار گرفته شد . صفحات سیمانی حاوی الیاف آزبست امروزه نیز تولید می شود. پس از آن آزبست بصورت مکمل استفاده شد و امروزه انواع مختلف الیاف سلولزی جانشین آزبست شده است . همچنین استفاده از الیاف مصنوعی که قادر به ارائه مشخصات خاص به محصول نهائی هستند متداول است .
دراین قسمت به ترکیبات جدید بر پایه سلولزی می پردازیم زیرا پایداری بهتری دارند . الیاف سلولزی برحسب نوع چوبی که بکار گرفته می شود تا ۴ میلی متر طول دارند. الیاف چوبهای که معمولا مصرف می شود ۳ میلی متر است . قطر الیافه سلولزی ممکن است با یکدیگر فرق کند اما اختلاف قطر بین انواع مختلف ناچیز است و بطور معمول حدود ۴۰ میکرون می باشد.
در این مرحله منبع الیاف و شکل گیری الیاف فاقد اهمیت می باشد . شکل گیری فیلم به مشخصات هیدرولیکی آنها بستگی دارد.
مواد غیرالیافی :
مواد خاصی که علاوه بر سیمان پرتلند در سمنت برد های امروزی استفاده می شود به مشخصاتی که برای محصول نهائی در نظر گرفته می شود بستگی دارد. دو گروه اصلی صفحات سیمانی با الیاف سلولزی وجود دارد . خشک شده (Cured ) با حرارت پایین که به هوا خشک معروف شده است و خشک شده (Cured) با حرارت بالا یا به وسیله اتو کلاو . ترکیب در روش هوا خشک معمولا حاوی مقدار زیادی سیمان پرتلند که با موادی مانند خاک رس، میکرو سیلیکا، سنگ آهک یا خاکستر است که به نسبت های دقیقی ترکیب می شود. ترکیب در روش اتو کلاو معمولا شامل سیلیس کاملا نرم شده همراه با سایر مواد مصرفی کاملا نرم بوده و مقدار کمتری سیمان دارد.
به استثناء خاک رس و میکرو سیلیکا که ممکن است ذراتی به اندازه ۲ میکرون یا کمتر داشته باشد معمولا میانگین قطر مواد غیرالیافی حدود ۵۰ میکرون می باشد که برابر با سیمان پرتلند است این نکته در شکل گیری فیلم حائز اهمیت می باشد.
شکل گرفتن لایه فیلتر ( لایه اولیه الیاف چسبیده به غربال )
معمولا منافذ غربال حدود ۰.۴ میکرون می باشند و واضح است که مواد غیرالیافی درحد قابل توجهی از منافذ غربال کوچکتر بوده و از غربال می گذرند. درحالیکه الیاف می توانند روی منافذ قرار گیرند مگر اینکه بر سطح غربال عمود شوند که دراین حالت می توانند از منافذ غربال عبور کنند. بنابراین جمع شدن مواد غیرالیافی بستگی به شکل گرفتن لایه الیاف برسطح غربال دارد. الیاف این لایه رامی توان را به وضوح درسطح رویه صفحات که دریک ماشین هات چک سرریزی شکل گرفته مشاهده کرد ، اگرچه این امر در صفحاتی که در ماشین دارای دیگ ثابت یا غیر سرریزی شکل گرفته خیلی روشن نیست.
راندمان جذب مواد غیر الیافی توسط لایه فیلترشده الیاف بستگی به یکدست بودن الیاف دارد .
عمل آوری الیاف خام جهت کاهش قطر موثر آنها ضرورری است ، این عمل از طریق یک فرایند تصفیه که در آن بجای بریدن الیاف آنها را له می کنند انجام می شود. طی فرایند تصفیه ساختار داخلی الیاف را خرد کرده و آنرا انعطاف پذیرتر می کند، هنگامیکه نرمی الیاف بیشتر می شود و شعاع هیدرولیک کاهش می یابد (شعاع آبى که برابر است با سطح خیس شده به محیط خیس شده) شرایطی ایجاد می شود که الیاف به هم پیچیده و گره بخورند .
برخی از انواع الیاف چوب را می توان تقسیم نمود (برش داد) و همچنین می توان از آنها شبکه نازکی را به وجود آورد . حاصل کار این است که الیاف سلولزی پس از تصفیه قادرهستند شبکه ای از الیاف نازک جهت جذب ذرات درشتر غیر الیافی به وجود آورند . به این صورت لایه فیلتر اولیه بر سطح غربال تشکیل شده و امکان شکل گیری فیلم را فراهم می نماید.
باید به این نکته توجه نمود که تصفیه الیاف مصنوعی که مصرف آن در ترکیب هواخشک ها متداول است معمولا امکان پذیر نیست . الیاف مصنوعی دارای ساختار یکنواخت می باشند و تصفیه به جای گسترش سطوح آنها را می برد . تنها تصفیه سلولز هایی که از چوب بدست می آید امکان پذیر است زیرا ساختار درونی پیچیده الیاف چوب است که توانایی جذب و انتشار انرژی تصفیه کردن را بدون ایجاد خسارت یا بریدن الیاف را دارا می باشد . بنابراین فرمولاسیون هواخشک ها حاوی حداقل مقدار سلولز برای شکل گرفتن فیلم است هر چند که به مشخصات مکانیکی صفحات الیاف دار نهایی کمک چندانی نمی نماید.
الیاف پس از شکل گرفتن لایه فیلتر جذب ذرات غیر الیافی را آغاز می کنند و ذرات به نوبه خود فضاهای بین الیاف را پر می نما یند . به این ترتیب اندازه منافذ فیلم سریعا کاهش یافته و ریزترین ذرات غیر الیافی نیز در فیلم جذب می شوند .
بنابراین ، فیلم دارای ساختاری است که روی سطح غربال غنی از الیاف بوده و در سطح دیگر الیاف نسبتا کمتری وجود دارد. این ساختار در تمام فیلم ها یکسان بوده و به همین صورت پس از شکل گیری در محصول نهایی – به دلیل این واقعیت که فیلم با الیاف تقویت شده- همچنان باقی می ماند . الیاف مانع تغییر شکل فیلم در فرایند تولید می شوند . بنابراین ، اگر چه ممکن است مقدار اندکی از مصالح با دانه بندی ریز تر از محلشان جابجا شده و در داخل فیلم ته نشین شود ، این مقدار جزئی بوده و تناسب مصالح با دانه بندی مختلف در موقعیت های مختلف پایدار می ماند .نظریه فلیتر شدن بر تشکیل فیلم در ماشین هات چک دلالت می کند .
درصورت تمایل به این مطلب امتیاز دهید:
دیدگاه خود را ثبت کنید