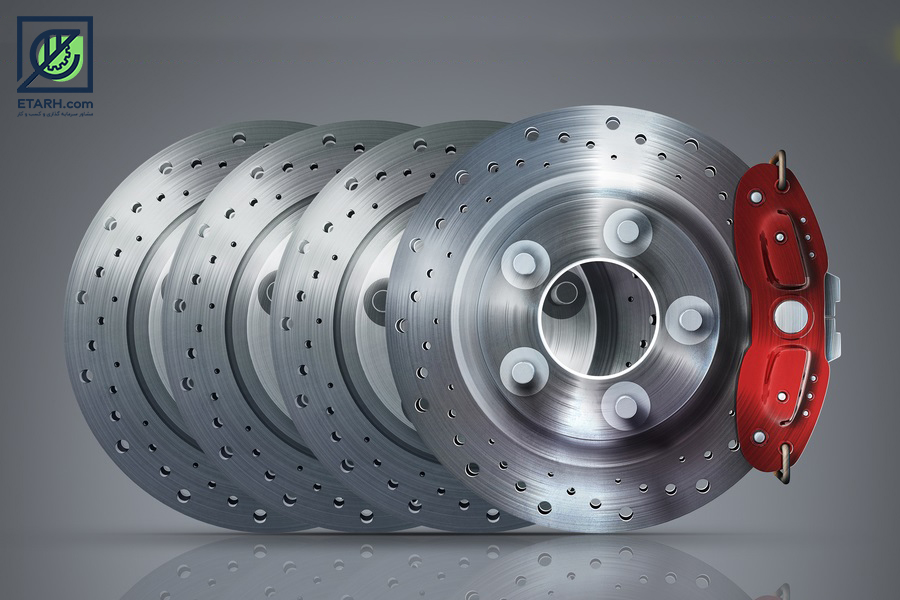
طرح تولید دیسک ترمز خودرو
- 9 خرداد 1401
- ۰
- بازدیدها: 1,765
- دسته بندی:
طرح تولید دیسک ترمز خودرو
اکثر خودروهای مدرن دارای ترمزهای دیسکی در چرخ های جلویی هستند و برخی نیز دارای دیسک ترمز در هر چهار چرخ هستند. این بخشی از سیستم ترمز است که کار توقف خودرو را انجام می دهد. متداول ترین نوع دیسک ترمز در اتومبیل های امروزی، کالیبر شناور تک پیستونی است. نام دیگر این قطعه دیسک چرخ است و با توجه محل قرار گیری آن که ما بین چرخها و لنت ترمز است ظاهری دایرهای شکل دارد. این قطعه را از جنس آلومینیوم، فولاد، چدن یا آهن میسازند و لنت ترمز با ایجاد اصطکاک بر روی آنها به کمتر شدن سرعت یا توقف کامل اتومبیل کمک میکنند. دیسک را توسط چند پیچ به قسمت مربوط به خود بستهاند که این کار به سادگی صورت گرفته است. همچنین از دیگر قطعات به کار رفته در این بخش میتوان به کالیپر ترمز و سیلندر اصلی اشاره کرد.(طرح تولید دیسک ترمز خودرو)
درک عملکرد این بخش زیاد هم سخت نیست، هنگامی که پدال ترمز فشرده شود پدهای لنت با دیسک چرخ برخورد میکنند و این کار باعث ایجاد اصطکاک و کم شدن سرعت چرخش دیسک ترمز میشود. به این ترتیب با کاهش سرعت دیسک ترمز سرعت چرخها هم کم میشود تا در نهایت اتومبیل به توقف کامل برسد. دیسکهای ترمز استفاده گستردهتری دارند. دیسکهای ترمز به دلیل در تماس بودن بیشتر با جریان هوا نسبت به کاسههای ترمز، قابلیت خنکشوندگی بهتری دارند. با توجه به دلایل مذکور و برخی از مزایای دیگر دیسکهای ترمز، انتخاب مناسبی برای سیستم ترمز جلوی خودروها در صنعت خودروسازی محسوب میشوند.
برای طراحی مناسب سیستم ترمز مؤثر، این مسئله بسیار مهم است که حرارت ایجاد شده تا جایی که ممکن است، بهسرعت پراکنده شده و از بین برود. در غیر این صورت ممکن است دمای دیسک ترمز افزایش یافته و بر عملکرد دیسک ترمز تأثیر بگذارد. در این مقاله دو موضوع، جنس و نوع دیسک ترمز از نظر فیزیک و ظاهر بر نحوه انتقال حرارت به اختصارتوضیح داده میشود.
مواد استفاده شده در دیسکهای ترمز میبایستی قابلیت جذب و دفع حرارتهای تولید شده در حین ترمزگیری و مقاومت در برابر خستگی حرارتی و سایش را داشته باشند. در حین ترمزگیری در اثر اصطکاک ایجاد شده در فصل مشترک بین سطوح لنت و دیسک در مدت زمان کوتاهی در این ناحیه دما به حدود ۸۰۰ درجه سانتیگراد میرسد که موجب ایجاد گرادیان دمایی در سطح دیسک تا مرکز دیسک میشود که این شیب دمایی به ۵۰۰ درجه سانتیگراد میرسد. پس از مدت زمانی این حرارت به محیط اطراف دیسک منتقل شده و در نهایت دمای دیسک کاهش مییابد.(طرح تولید دیسک ترمز خودرو)
به دلیل حضور فاز گرافیت در ساختار چدنهای خاکستری، این نوع چدنها از هدایت حرارتی مناسبی برخوردارند که موجب بهبود خاصیت هدایت حرارتی آنها میشود. اکثر دیسکهای ترمز رایج، از چدن خاکستری با زمینه غالباًً پرلیتی تولید میشوند. گرافیتهای لایهای چدن خاکستری، به شکل تیغههای به هم پیوستهای هستند که مسیری مناسب برای استخراج و خروج سریع حرارت ایجاد میکنند.
بر خلاف چدنهای خاکستری در چدنهای نشکن، ذرات گرافیت نشکن بهصورت مجزا و منقطع هستند و از یکدیگر مستقلند و سهم کوچکی برای انتقال حرارت در این نوع چدنها دارند. به همین دلیل انتقال حرارت چدنهای نشکن بسیار کمتر از چدنهای خاکستری است.
گرافیتهای کرمی شکل در چدنهای گرافیت فشرده (چدن با گرافیت کرمیشکل) ۳CGI نیز نظیر چدنهای خاکستری به هم پیوستهاند، اما به علت شکل گرافیت از نظر خواص مکانیکی و حرارتی بین چدنهای خاکستری و نشکن قرار دارند. به بیان دیگر، خواص مکانیکی بهتری نسبت به چدنهای خاکستری و کمتری نسبت به چدنهای نشکن دارند و هدایت حرارتی کمتری نسبت به چدنهای خاکستری و بیشتری نسبت به چدنهای نشکن دارند. چدنهای CGI امروزه صرفاً بهعنوان مواد جایگزین محسوب میشوند و به دلیل دانش فنی محدود، تا به حال توسط صنعت خودروسازی به طور کامل بررسی نشدهاند.
دیسک ترمز یک صفحه نازک آهنی است که بین چرخ و جایی که بلبرینگ قرار دارد واقع شدهاست. بیشتر ماشینهای جدید (ماشینهای تولیدی از سال ۱۹۹۹ به بعد) روی هر چرخ یک دیسک ترمز دارند در حالی که ماشینهای قدیمی فقط از دو دیسک در چرخ عقب استفاده میکردند. دیسک (چرخنده) ترمز نقش بسیار مهمی در سیستم ترمز ایفا میکند به گونه ای که باعث اصطکاک میان لنت و دیسک شده و همین امر باعث کاهش سرعت و در نهایت ایستادن خودرو میشود. به هنگام از کار افتادن دیسک ترمز (نازک شدن یا کج شدن) آنها قادر به خارج کردن گرمای ناشی از ترمز کردن از سیستم ترمز نیستند و همین عامل سبب سرخ شدن دیسک و کاهش تأثیرگذاری سیستم ترمز میشود.(طرح تولید دیسک ترمز خودرو)
اجزای اصلی دیسک ترمز عبارتند از:
لنت های ترمز
کالیبر که شامل یک پیستون است
روتور یا قسمت گردنده ماشین که بر روی توپی چرخ سوار شده است
دیسک ترمز بسیار شبیه ترمزهای دوچرخه است. ترمزهای دوچرخه دارای کالیبر هستند که باعث می شود لنت های ترمز در برابر چرخ فشرده شوند. در دیسک ترمز، لنت های ترمز به جای چرخ، روتور را فشرده می کنند و نیرو به جای هیدرولیک به کابل انتقال می یابد. اصطکاک بین لنت ها و دیسک باعث پایین آمدن دیسک می شود.
دیسک ترمز چیست و چه وظایفی دارد؟
دیسک ترمزدیسک ترمز در واقع قطعه ای دایره ای در قسمت چرخ ها است که وظیفه آن متوقف ساختن خودرو در هنگام گرفتن ترمز می باشد. این قطعه حیاتی در خودرو دارای یک طول عمر مشخص است و پس از طی این مدت، رفته رفته از کارایی آن کاسته می شود. دیسک ترمز با دو قطعه دیگر خودرو ارتباط مستقیم دارد. اول با چرخ ها که همگام با آن ها شروع به چرخش کرده و همگام با آن ها از حرکت باز می ایستد. دومین قطعه ای که مستقیما با این دیسک در ارتباط است، لنت ترمز بوده که پیش از این در رابطه با آن مفصلا صحبت کرده و وظایف آن را به طور کامل بررسی کرده ایم. هنگامی که راننده پای خود را روی پدال ترمز فشار می دهد، لنت ها با دیسک ترمز درگیر می شوند و در نتیجه باعث می شوند تا از سرعت چرخش دیسک کم شود. کم شدن سرعت گردش دیسک ها سبب می شود تا چرخ ها نیز سرعتشان کاسته شود و در نهایت به طور کامل از حرکت باز ایستند. اگر دیسک ترمز به درستی عمل نکند و کارایی مناسبی نداشته باشد، در نتیجه در هنگام ترمز گیری، خودرو عملکرد مناسبی نخواهد داشت و در نتیجه دچار مشکل خواهد شد.(طرح تولید دیسک ترمز خودرو)
جنس دیسک ترمز چیست؟
به طور کلی، نوع آلیاژ بکار رفته در تولید دیسک های ترمز به سبب فاکتور هایی از جمله تفاوت کارایی، طول عمر، قیمت و کیفیت متفاوت است. دیسک ترمز به سبب اینکه دائم در اصطکاک و حرارت بالا قرار دارد، معمولا از جنس چدن خاکستری یا سرامیک کربن است.
دیگر آلیاژ های بکار رفته در تولید دیسک ها عبارتند از:
فولاد ضد زنگ
تیتانیوم
کامپوزیت ماتریکس آلومینیوم
امروزه استفاده از دیسک ترمز هایی که از فولاد ضد زنگ ساخته میشوند از محبوبیت بالاتری برخوردار است چرا که دارای ویژگی هایی از جمله موارد زیر هستند:
مقاومت در برابر حرارت بالا
جوش پذیری
حرارت قابل کنترل
هزینه تولید پایین
استحکام بالا
مقاوم در برابر خوردگی
انواع دیسک ترمز
دیسک ترمز معمولی
این نوع دیسک ترمز ها به شکل کاملا ساده طراحی شده اند و دارای سطح صاف و صیقلی شده هستند. نام دیگر این دیسک ترمز های معمولی Solid میباشد. آهن مهم ترین آلیاژ در تولید این نوع دیسک ترمز است که دارای ضریب حرارتی بالایی نیست. به همین دلیل، خودرو هایی که از دیسک ترمز معمولی بهره میبرند معمولا قابلیت ترمزگیری خوبی ندارند. این دیسک ها خصوصا در خودرو های دارای سیستم ضد قفل به راحتی داغ میشوند و دارای یک صفحه آهنی توپر هستند.
دیسک ترمز خنک شونده
این مدل دیسک ترمز که با خنک شونده هم شناخته میشود از اشکال متفاوتی برخوردار است. همین اشکال مختلف در طراحی آنها سبب میشود تا در هنگام ترمزگیری کمی از گرمای تولید شده را از خود دفع کنند که به کمک مکانیزمی که برای حرکت هوا در اطراف آن تعبیه شده صورت میگیرد.
دو وجه صفحه در این دیسک ترمز ها از هم جدا شده و تبدیل به صفحه ای توخالی میشود تا تعبیه کانال های خنک کننده در درون آنها وجود داشته باشد. این پروسه خنک کنندگی به کاهش حرارت کالیبر نیز کمک شایانی میکند. در این نوع دیسک ها سیستم ترمز به خوبی عمل کرده و کاهش ترک خوردگی دیسک را نیز به همراه دارد.
دیسک ترمز های خنک شونده خود نیز دارای انواع مختلفی است:
دیسک های سوراخ دار
سطح این دیسک ها دارای سوراخ هایی است که به منظور خروج حرارت ناشی از درگیری ترمز و لنت ها و کاهش اصطکاک است. دلیل دیگر وجود این سوراخ ها برای خروج گازهایی است که مواد موجود در لنت در زمان درگیری دیسک از خود متصاعد میکند.
خروج و تخلیه این حرارت و گاز ها در نهایت عملکرد بهتر سیستم ترمز را در پیش دارد. اما وجود آنها موجب ضعف در عملکرد دیسک ها میشود.
دیسک های شیاردار
شیار هایی بر روی این نوع دیسک تراش داده میشود که عمل انتقال گاز، آب، و حرارت را از روی سطح دیسک مدیریت میکند. بنابراین، مواد مضر تشکیل شده ناشی از اصطکاک لنت و دیسک از طریق این شیار های خارج میشوند. استفاده از دیسک های شیاردار معمولا در خودرو های مسابقه ای مرسوم است و توان مقابله با فشار های بالا را دارا هستند.
دیسک های مختلط
شیار و سوراخ با هم بر روی این نوع دیسک ها تعبیه شده است که در کنار حفظ یکپارچگی دیسک، آب، گاز، و حرارت از سطح آنها منتقل میشود و اصطکاک لنت ها را کاهش میدهد.
دیسک های موج دار
وزن این دیسک ها بسیار کمتر از انواع دیگر است و تخلیه حرارتی بهتری را شامل میشود. صفحه خارجی این نوع دیسک دارای کنگره های موجی است و دوسطح آن نیز سوراخ دار میباشد. یک صفحه کوچکتر شیادار نیز بین دو صفحه آن قرار میگیرد و استحکام آن را افزایش میدهد.
این دو سطح تنها در مرکز به هم متصل هستند و اتصالی در بین محیط آنها وجود ندارد. دیسک های موج دار قبلا بر روی موتور های مسابقه ای بکار میرفت اما کمپانی آئودی تصمیم بر استفاده از آنها بر روی خودرو های خود گرفت.
دیسک یکپارچه (Solid Disc)
ساده ترین دیسک موجود در بازار دیسک یکپارچه است. ساختار آن ها مانند یک بلوک یکپارچه فلزی است، از این رو تولید آن بسیار ساده و ارزان است، به همین دلیل ارزان ترین دیسک موجود در بازار است. مشکل اصلی این نوع از دیسک ها تبادل حرارتی آن هاست. این دیسک ها به علت این که به صورت یکپارچه قالب گیری می شوند، کاملاً از فلز تشکیل شده اند، سنگین اند و هیچ هوایی وارد قسمت میانی آن ها نمی شود و به همین دلیل به راحتی خنک کاری نمی شوند. این عیب باعث می شود به کلیپر آسیب برسد و مصرف لنت نیز افزایش یابد.
دیسک مجرادار (Vented Disc)
امروز تقریباً در همه خودروهای تولیدی دنیا از دیسک هایی استفاده می شود که بین لایه بیرونی و درونی آن فضایی خالی ایجاد شده است تا هوا بین دو لایه از دیسک جریان یابد و به این ترتیب از دمای مجموعه کاسته شود. بین دو لایه دیسک بیرونی و درونی کانال هایی برای عبور هوا طراحی شده اند، این کانال ها باعث می شوند گرمای تولیدشده در اثر اصطکاک بین دیسک و لنت، در مجموعه باقی نماند و توسط هوای در جریان از مجموعه خارج شود. وجود این کانال ها باعث می شود دیسک بیش از اندازه گرم نشود و به دنبال آن ترک برندارد و همچنین از مصرف لنت نیز کاسته می شود.
در طول زمان شکل و شمایل کانال های درون دیسک تغییر یافته است، این تغییرات در راستای کاهش حداکثری دما صورت گرفته است و اساس آن ها علم سیالات و انتقال حرارت است.
دیسک حفره دار (Drilled Disc)
در برخی از خودروها، بر حسب کاربردی که دارند، ترمزگیری های شدیدی اتفاق می افتد، در اثر این ترمزگیری های شدید گرد و گازهایی در اثر تماس لنت با دیسک تولید می شود که انباشته شدن این محصولات بین دیسک و لنت موجب می شود بازده سیستم ترمز کاهش یابد. با توجه به بروز چنین مشکلی، روزنه هایی بر روی دیسک ها به وجود می آورند تا گرد و گازهای حاصل از فضای بین لنت و دیسک تخلیه شود. به این ترتیب، هم بازده ترمزگیری بهتر می شود و هم به دلیل ایجاد روزنه ها، از وزن دیسک کاسته می شود. با حفره دار کردن این دیسک ها از مساحت آن ها کاسته می شود، کاهش در مساحت دیسک موجب می شود تبادل حرارتی کم تری صورت گیرد و به همین ترتیب، دمای مجموعه افزایش می یابد. یکی دیگر از ویژگی های منفی این دیسک ها وجود نقاط حساس در اطراف حفره هاست که موجب می شوند در اثر قرار گرفتن تحت تنش زیاد، دیسک دچار ترک شود. امروز لنت ها از موادی ساخته می شوند که گرد و گاز کم تری در خود دارند، به همین دلیل به کارگیری این نوع از دیسک ها نیز کم تر می شود. اما همچنان شاهد هستیم که در بسیاری از خودروهای پرقدرت از این دیسک ها استفاده می شود، زیرا هم جذابیت خاصی به خودرو می بخشند و هم ساخت آن ها به گونه ای است که به ندرت پیش می آید دچار شکست شوند.
دیسک چرخ یا دیسک ترمز چه کاربردی دارد و چگونه کار میکند؟
همان طور که گفته شد، اصلیترین وظیفهی قطعهی دیسک متوقف ساختن ماشین با کمک نیروی اصطکاک است. اگرچه جنس چدنی و سرامیکی قطعهی دیسک، از فرسایش آن در کوتاه مدت جلوگیری میکند، این قطعه نیز مانند سایر قطعات خودرو بهتدریج کارایی خود را از دست میدهد. توجه کنید که دیسک و لنت نیز با یکدیگر ارتباط مستقیم دارند. این لنت ترمز است که پس از فشرده شدن پدال ترمز، با قطعهی دیسک درگیر شده و با تغییر فشار روغن ترمز آن را وادار به متوقف شدن میکند. یکی از شایعترین علامتهای از کار افتادگی قطعهی دیسک، افزایش مسافت توقف است.
چه آلیاژهایی برای ساخت دیسک ترمز بسیار مناسب هستند؟
کربن
چدن
فولاد (ضد زنگ)
تیتانیوم
ترکیبات آلومینیوم
دیسک ترمز کربنی
دیسک ترمزهایی که در مواد اولیه آن ها درصدی از کربن استفاده می شود دارای بهترین ضریب حرارت می باشند.
کربن باعث می شود که هنگام که راننده ترمز می کند حتی ترمزگیری های خیلی سخت، دیسک ترمز عالی ترین عملکرد خود را نشان دهد و درصد تغییر شکل دیسک چرخ و هم چنین خم شدن آن که منجر به بروز حوادث ناگوار می شود به حداقل برسد.
در دو وجه دیسک ترمز که مورد اصطکاک قرار می گیرد، کربن به کار می رود.
استفاده از کربن در ساخت دیسک ترمز دارای مزایایی می باشد که عبارتند از:
افزایش کارایی سیستم ترمز
تحمل حرارت بالا
کاهش وزن
مقاومت در برابر ساییدگی
افزایش طول عمر دیسک ترمز
افزایش کنترل فرمان توسط راننده
احساس راحتی هنگام فشردن پدال ترمز خودرو
دیسک ترمز چدنی
نقطه ذوب چدن بسیار پایین و ظرفیت آن بالا می باشد و علاوه بر آن این آلیاژ به خوبی ماشین کاری می شود. دیسک ترمز هایی که با چدن ساخته می شوند در برابر خوردگی بسیار مقاوم هستند و به راحتی ساییده و از بین نمی روند. همچنین آلیاژ چدن به کار رفته در دیسک ترمز دارای ضریب انتقال حرارت مناسب است.
دیسک ترمز فولادی
دیسک ترمز های ساخته شده از فولاد دارای مقاومت بالا اند و و جزء دیسک ترمز های خوب محسوب می شوند. لازم به ذکر است که هزینه تولید آن از سایر مواردی که گفته شده ارزان تر است و در خودروهای ارزان قیمت از فولاد استفاده می شود.
دیسک ترمز تیتانیومی
دیسک ترمز های تولید شده از تیتانیوم همانند دیسک ترمز های کربن دار، کیفیت بسیار بالایی دارند. اما لازم به ذکر است که استفاده از این ماده برای تولیدکنندگان بسیار پرهزینه می باشد و به همین دلیل از تیتانیوم در تولید دیسک ترمز خودروهای لاکچری استفاده می شود.
دیسک ترمز آلومینیومی
دیسک ترمزهای آلومینیومی دارای مزیت هایی همچون سبکی وزن، ضریب انتقال حرارت عالی، طول عمر نسبتا عالی و … می باشند. دیسک ترمز های آلومینیومی علاوه بر مزیت هایی که در بالا گفته شد دارای معایبی نیز هستند که یکی از آن ها کم بودن استحکام دیسک ها می باشد و نسبت به سایر دیسک ها سریع تر از بین می روند.
کد آیسیک مرتبط با صنعت تولید دیسک ترمز خودرو
کد آیسیک مخفف International Standard Industrial Classification (سیستم بین المللی طبقه بندی استاندارد صنایع) است. کد گذاری به عنوان روش ساده و دقیق برای تعیین هویت کالا، قطعات ، مدارک و اموال ، سالها است که در سطح شرکت هاو زنجیره های تأمین مورد استفاده قرار می گیرد.
با توجه به بررسی های انجام شده کد آیسیک دیسک ترمز خودرو به شرح جدول ذیل می باشد
شرح محصولات | کد آیسیک |
دیسک ترمز خودرو | ۳۴۳۰۴۱۲۴۹۷ |
دیسک ترمز خودروی سبک | ۳۴۳۰۵۱۲۴۹۸ |
دیسک ترمز خودروی سنگین و نیمه سنگین | ۳۴۳۰۵۱۲۵۷۴ |
کد تعرفه گمرکی مرتبط با صنعت تولید دیسک ترمز خودرو
تعرفه یا به عبارت دیگری(TARIFF) یک نوع معیار رقمی و یا عددی می باشد برای شناسی و تعیین جایگاه کالا در ترخیص کالا .
تعرفه گمرکی میزان حقوق ورودی قابل پرداخت برای ورود کالا می باشد.تعرفه گمرکی در بستر تاریخ مبتنی بر سیستم و روش های خاصی از قبیل اداره گمرک،آمار،حمل و نقل،بیمه و غیره طراحی و مورد استفاده قرار می گیرد.
با توجه به بررسی های انجام شده کد تعرفه گمرکی دیسک ترمز خودرو به شرح جدول ذیل می باشد
شرح محصول | کد تعرفه گمرکی |
دیسک ترمز خودرو | ۸۷۰۸۳۰ |
فرایند ریختهگری
فرایند ریختهگری تمامی قطعات دیسک و کاسههای ترمز به روش ریختهگری در قالب ماسهایتر و توسط دستگاه ریختهگری دیزاماتیک انجام میشود. اجزای این دستگاه عبارتند از:
۱. خط قالبگیری
۲. کوره پورینگ
۳. خط خنککاری (کانوایر)
۴. سند کولر
۵. نوار تخلیه
سیستم قالبگیری این دستگاه به این صورت است که مخلوط ماسه قالبگیری که از ماسه سیلیسی برگشتی، ماسه جدید، پودر زغال، آب و بنتونیت تشکیل شده است توسط هوای فشرده بین دو صفحه مدل که بهصورت عمودی و موازی نسبت به هم قرار گرفتهاند فشرده و قالب تشکیل میشود. سپس قالب توسط جکی به سمت جلو و زیر نازل، محلی که عمل ذوبریزی مذاب توسط کوره پورینگ انجام میشود هدایت میشود.
کوره پورینگ، کوره القایی هستهداری شامل سیمپیچ اولیه، پوشیده شده بهوسیله مواد نسوز است که به نحوی در کوره قرار گرفتهاند که یک کانال در اطراف آن تشکیل شود. این سیمپیچ به دور یک هسته تشکیل شده از لایههای آهن پیچیده شده و به بدنه کوره متصل شده است. از کورههای القایی هستهدار معمولاً بهمنظور نگهداری مذاب، افزایش فوق ذوب، تصفیه و همگن کردن مذاب و ریختهگری پیوسته قطعات استفاده میشود. فرایند ذوبریزی در اتاق کنترل توسط اپراتور پورینگ، استپر کوره به سمت بالا هدایت شده و مقدار ذوب معین شده در زمان و دبی مناسب و تعیین شده به داخل قالب بارریزی خواهد شد. در حین بارریزی، عمل جوانهزنی به سمت جریان مذاب انجام میشود. عملیات جوانهزنی مذاب سایز سلولهای یوتکتیکی را کاهش داده و محدوده رشد گرافیت در داخل هر سلول قرار خواهد گرفت. بنابراین استحکام قطعه ریختهگری را افزایش میدهد. پس از پر شدن قالب از مذاب، قالبها پشت سرهم بر روی نوار کانوایر خنککننده قرار خواهند گرفت و تا سند کولر مسیری را طی میکند تا فرصت منجمد شدن قطعه ایجاد شود. پس از منجمد شدن قطعه قالب به داخل سندکولر هدایت شده که تخلیه قالب و جداسازی سیستم راهگاهی از قطعه انجام شود. پس از تخلیه قالب، قطعات بر روی نوار تخلیه ریخته شده و بر روی این نوار جداسازی قطعات از سیستمهای راهگاهی انجام میشود. پس از جداسازی، قطعات به منظور تمیزکاری و پرداخت، وارد واحد شات بلاست شده و سطح قطعات به وسیله پرتاب و شوت ساچمههای فولادی با سرعت و حجم بسیار از ماسههای باقیمانده از قالب ریختهگری عاری شده و قطعه تمیز از اتاق شاتبلاست خارج میشود. پس از پرداخت به منظور حذف محل اتصال سیستم راهگاهی، ونت هوا و تغذیه از قطعه این محلهای سنگزنی شده و قطعه پس از کنترل نهایی و بازرسی نهایی به انبار محصول تحویل داده میشود.(طرح تولید دیسک ترمز خودرو)
قیمت دیسک ترمز خودرو در بازار
عوامل زیادی در تعیین قیمت دیسک ترمز برای خودرو نقش دارند. از جمله میتوان به کیفیت و دوام این قطعه اشاره کرد. یکی از فاکتورهای مهم در تعیین قیمت دیسک چرخ، کیفیت و دوام بالای محصول است. در محصولاتی که از آلیاژ فولاد بدون ناخالصی استفاده میشود، مدت زمان استفاده از دیسک خودرو بیشتر است. به طوری که تا چندین سال به تعویض آن نیاز ندارید. همچنین طراحی خنککننده هم در افزایش قیمت دیسک ترمز مؤثر است. نوع برند هم در تعیین قیمت مؤثر است.(طرح تولید دیسک ترمز خودرو)
پیش بینی وضعیت سرمایه گذاری طرح تولید دیسک ترمز خودرو
ظرفیت تولید سالیانه: ۱۰۰.۰۰۰ عدد
نرخ برابری دلار: ۳۰۰۰۰ تومان
مساحت زمین موردنیاز: ۲۵۰۰ مترمربع
زیربنای کل: ۱۲۰۰ مترمربع
تعداد نیروی انسانی مورد نیاز: ۲۶ نفر
میزان سرمایه گذاری ثابت: ۳۰ میلیارد تومان (بدون احتساب هزینه زمین)
ارزش ماشین آلات و تجهیزات: ۱۴ میلیارد تومان
نرخ بازده داخلی در سال مبنا: ۳۹ درصد
دیدگاه خود را ثبت کنید